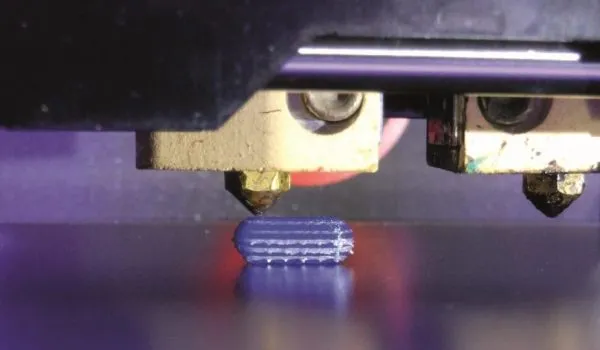
3D Pharmaceuticals Printing is the process of creating solid objects using a 3D printing machine, raw base materials, and a digital file. The process is positioned to transform the production process throughout the supply chain across all manufacturing sectors, including pharmaceuticals.
The benefits of 3D printing technology for the pharmaceutical industry are numerous. They include the ability to create specialized batches of customized 3D printed medicines, precision dosages, customized sizes, varying shapes, and release mechanisms.
As the concept of “personalized medicine” continues to gain ground across the pharmaceutical space, 3D pharmaceuticals printing is positioned to play a leading role in industry transformation. Along with refining production and supply mechanisms, 3D medicines printing is poised to catalyze the increased use of customised medicines for precision treatments.
What is 3D Printing?
3D printing (also known as “additive manufacturing”) is a process that refers to the production of solid three-dimensional objects using a 3D printing machine and specialized digital file. The 3D printing machine uses additive processes where layers are applied to each other to create the final object.
3D printing has existed for decades, and was used predominantly for prototyping and one-off manufacturing until its transformation into a production technology. Acumen Research and Consulting forecast the global market for 3D printing to reach $41 billion by 2026.
How 3D Printing Works
The additive manufacturing technique starts with a 3D model that can either be created from scratch or downloaded from a 3D library. The model is then used with a 3D software application that can either be purchased or downloaded from an open-source platform. Once the printable file is created, it must be prepared for the 3D printer through a procedure called “slicing”.
Slicing refers to a process that literally “slices” the 3D model into hundreds or thousands of layers that are then read by the 3D printer via Wi-Fi, SD or USB. These layers are then created with the use of base materials to produce the object.
Get your requested raw materials quotation
3D Printed Medication in Pharmacology
The first FDA-approved medication produced via 3D printing was created by Aprecia Pharmaceuticals in 2015. This was followed in 2017 by GlaxoSmithKline with a study that used ultraviolet (UV) curing and inkjet 3D printing to produce tablets for Parkinson’s disease.
Money continues to pour into research for 3D pharmaceuticals. Along with this increased investment, new companies are entering the space and conducting ground-breaking research that is leading to the creation of new drugs for precision medical treatments.
Get your requested raw materials quotation
Pharmaceutical 3D Printing Methods
New innovations in 3D printing are focused on drug design, material properties and development processes. The 3D-printed medicines that have been created to date have achieved innovation in all three areas for the purpose of creating personalised drug dosing for customized medical treatments.
When compared to traditional manufacturing, 3D printed pharmaceuticals are relatively easier to create and personalize. This allows producers to cost-effectively create smaller batches through the use of various methods that include:
Inkjet Printing
The inkjet printing method uses powder that is applied as a substrate of varying drug combinations in variable layers. The “ink” used in the process is sprayed in various droplet sizes that are then dried to create the desired solid dosage form.
Thermal Inkjet Printing
Similar to inkjet printing, thermal inkjet printing uses ink fluid and a micro-resistor to create a vapour bubble. This “ink” is then dispensed through a nozzle as a solution onto three-dimensional scaffolds. Thermal inkjet printing is a preferred method used to print heat-sensitive medications.
Fused Deposition Modeling
The fused deposition modeling process uses polymers that are melted down and then pushed through a heated, mobile nozzle. The polymers are then layered according to the X, Y, and Z axes specific to the 3D model. This technique is used predominantly for zero-order release tablets and implants, and other polymer-specific formulations.
Direct-Wise
The direct-wise 3D printing method uses a pattern-generating device to create 3D microstructures, guided by a computer-controlled translational stage.
Zip Dose
The zip dose 3D printing method can produce personalised high drug-load 3D printed medicines using porous material that relies on high disintegration and dissolution levels.
Vat Photopolymerization
The vat photopolymerization or light-induced polymerization 3D printing method uses light irradiation to cure liquid resins in layers that provide controlled release. The process uses two-dimensional layers that are then cured into a hardened 3D structure with varying drug delivery potential.
Other Uses of 3D Printing in Healthcare
3D printing is increasingly being used in healthcare, particularly to produce implants. While some of these use-cases may be experimental, others are becoming more common – such as the creation of over 100,000 hip replacements by GE Additive.
Another dominant use case of 3D printing in healthcare is the production of hearing aids via a collaboration between Phonak (now part of Sonova) and Materialise. Together, these companies have produced nearly every hearing aid device in the last 17 years through the use of 3D printing and custom software.
Pharmacy 3D Printing FAQ
3D pharmaceutical printing refers to the process of creating pharmaceutical products using a 3D printing machine, base materials, and a digital file.
Some of the benefits of 3D pharmaceutical printing include the ability to create customized medicine batches, different sizes, varying shapes, customized dosages, and specialized release mechanisms.
The advantages of 3D-printed drugs include the ability to create specialized pharmaceutical products on-demand using raw materials, an on-site digital printer, and digital file.
3D printing technology is not expected to change the need for pharmaceutical companies. Manufacturers will still be required to order the bases for their printed pharmaceuticals through a licensed distributor. Rather than storing traditional medications in tablet form, the pharmacists of the future may have the base product in stock and then produce customized dosages based on the patient’s individual needs.
The answer to whether 3D printing can create new opportunities to produce and distribute illegal drugs is not clear at this time. The answer to this concern lies mainly in the potential for the 3D process to optimize the production process and reduce costs.
Get your requested raw materials quotation
Good Manufacturing Practice (GMP)
GMP practices are guidelines recommended by agencies that control licensing and authorization of both the manufacture and sale of cosmetics, food, beverages, dietary supplements, medical equipment and pharmaceutical products. They are put into place and enforced to ensure product quality and consistency among manufacturers.
MedicaPharma partners with GMP manufacturers and specialty labs globally to establish and maintain strong professional relationships. This allows us to source and provide the highest quality chemical products on the market.